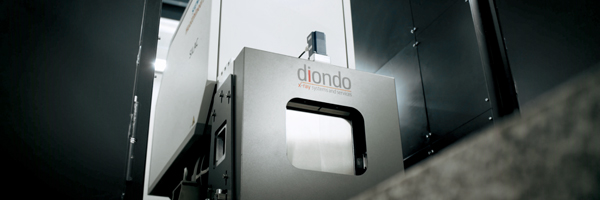
E-Mobility Demands Deep Insights into Materials
Non-destructive testing takes a look under the surface. The new application field of electrical mobility requires larger sample dimensions and challenging materials to be tackled. New innovations allow diondo to take on the challenge of inspection on the XXL-scale.
The industrial usage of X-ray Computed Tomography (CT) is a relatively recent development. The technical demands, and the costs of acquisition and operation of the required equipment, meant that for many years this method of quality control was the preserve of only the largest companies with the deepest pockets. Other companies had to make do with substantially less effective methods of testing products non-destructively.
Thanks to the further development of the technology and its growing prevalence, CT is now a tool of research and development, as well as quality control, accessible also to small & medium-sized enterprises (SMEs), in manufacturing in particular. CT is used both on site, integrated into the production process, and off-site, through CT service providers.
As a new branch of industry, E-mobility, including the development of novel propulsion technologies, is proving to be especially dependent on the outputs of modern inspection methods. The usage of novel materials and production methods in critical applications demands an exceptional level of quality control, attainable only through modern test methodologies such as CT. Defects in highly complex, sensitive and expensive components such as batteries, and other central elements of E-mobility such as rotors, not only present a safety risk to be avoided, but also entail costs to be minimised.
As Martin Münker, CEO of diondo GmbH, explains, “We have been pushing the bounds of industrial computed tomography for more than 25 years. It is obvious to us that the inspection demands only continue to grow – literally!”
Typical X-ray Computed Tomography systems are primarily suited for small to medium samples of low to moderate density. However, samples of high density materials, irrespective of size, readily show up the limits of conventional CT technology.
“Standard, “off the shelf”, CT solutions are typically unsuitable for the non-destructive examination of major E-mobility components, such as batteries or entire fuel cell assemblies.”, says Martin Münker. “We are witnessing a growing demand for large, powerful systems that can nonetheless perform precise inspections. Using industrial linear accelerators, deployed in customised systems, we are able to offer the appropriate solutions to support new technologies, for example in the aerospace sector, the field of additive manufacturing, or indeed E-mobility and novel energy sources.”
Industrial linear accelerators allow diondo to achieve a substantially higher performance compared to conventional X-ray sources, enabling a detailed insight into materials with densities beyond the imaging capabilities of conventional systems. The size of samples that can be inspected is a further differentiating factor between diondo’s offering and typical CT equipment.
An XXL-scale customised solution, built this year for a Chinese customer in the commercial vehicle sector, yet again has allowed diondo to demonstrate its competence in the field of exceptional CT solutions.
“The standard diondo d7 is already suitable for the examination of highly dense components of titanium, copper, steel or thick-walled aluminium, with dimensions up to 1000 x 1000 mm and a sample mass of up to 200 kg.”, notes Münker. “With our recent customised system we extend those possibilities by a multiple and reach a sample mass of up to one ton.”